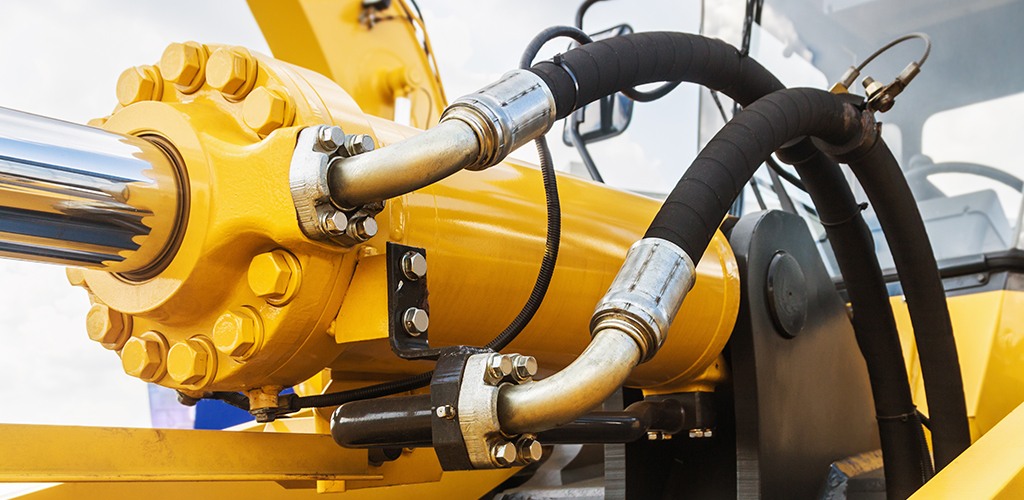
پنوماتیک
پنوماتیک یکی از انواع انرژی هایی است که در حال حاضر از آن استفاده زیادی در صنایع می شود و می توان گفت امروزه کمتر کارخانجات یا مراکز صنعتی را می توان دید که از سیستم پنوماتیک استفاده نکنند و در قرن حاضر یکی از انواع انرژی های اثبات شده ای است که بشر با اتکا به آن، بسیاری از نیازهای صنعتی خود را رفع می نماید.
پنوما در زبان یونانی یعنی تنفس باد و پنوماتیک علمی است که در مورد حرکات و تأثیرات هوا صحبت می کند.
در حال حاضر پنوماتیک در صنعت به عنوان انرژی بسیار تمیز و کم خطر و ارزان شناخته می شود و از آن به علت مزایا و خواصی مانند بازده بالا، قابل کنترل بودن و سادگی تعمیر و نگهداری آسان، در حجم زیادی استفاده می شود.
با گسترش و پیشرفت علم هیدرولیک و الکترونیک و کاربرد روز افزون آن ها در صنعت، سیستم های کنترل به سیستم های مدرن و پیشرفته ای چون سیستم پنوماتیک ارتقا پیدا کردند و از سیستم پنوماتیک یا نیوماتیک در مواردی که نیروهای نسبتاً پایین (حدود یک تن) و سرعت های حرکتی بالا مورد نیاز باشد (مانند سیستم هایی که در قسمت های محرک ربات ها به کار می روند) استفاده می کنند.
در صورتی است که کاربردهای سیستم های هیدرولیک بیشتر در مواردی است که قدرت های بالا و سرعت های کنترل شده دقیق مورد نظر باشد (مانند جک های هیدرولیک، ترمز و فرمان هیدرولیک).
- آلودگی بسیار پایین
- برخی موارد هزینه پایینتر
- طراحی ساده
- قابلیت افزایش نیرو
- سادگی و دقت کنترل
- انعطاف پذیری
- راندمان بالا
- اطمینان بالا


اجزا سیستم پنوماتیک:
1. فیلتر هوا
فیلتر هوا در ورودی کمپرسور قرار گرفته است، این فیلتر از ورود ذرات آلودگی با اندازه بزرگ به سیستم جلوگیری می کند و به کمک این تصفیه سازی از ورود بخش عمده ای از ذرات ناخواسته به سیستم و بروز ایرادات اساسی در سیستم جلوگیری می شود.
2. کمپرسور
وظیفه کمپرسور فشرده سازی هوای مورد نیاز سیستم تا فشار و حجم مشخص است.
کمپرسور انرژی مصرفی موتورش را به صورت انرژی ذخیره شده در هوای فشرده ذخیره می کند که متاسفانه تلفات این تبدیل انرژی بسیار بالاست.
رایج ترین نوع کمپرسور ها، کمپرسورهای اسکرو هستند و همچنین کپرسورهای پیستونی هم مورد استفاده قرار می گیرند.
لازم به ذکر لست این دستگاهها جز سبد کالاهای وارداتی و قابل تأمین شرکت کارینا صنعت نمی باشند.
3. خشک کن هوا و پیش فیلتر
وقتی هوا فشرده می شود دیگر نمی تواند رطوبتی در خود نگه دارد، بنابراین با فشرده کردن هوا کمی آب به وجود خواهد آمد.
از آنجایی که این آب حاصل از میعانات به بقیه سیستم آسیب می رساند باید از فرایند حذف شود و خشک کن های تبریدی می توانند این کار را انجام دهند.
همچنین خشک کن های جذبی هم هستند که آب را با مواد خاصی جذب می کنند.
این هوای فشرده معمولا با روغن کمپرسور یا ذراتی که در فیلتر ورودی جذب نشده اند هم آلوده می شود که موجب بروز اشکالاتی در سیستم پنوماتیک می شود مثل مشکلاتی که در شیرها ایجاد می شود که اغلب اوقات این ذرات توسط یک فیلتر مرکزی از هوای فشرده جداسازی می شود.
4. مخزن ذخیره هوا
از مخزن ها برای ذخیره موقت هوای فشرده استفاده می شود.
ذخیره سازی هوا، تامین تقاضای هوای فشرده را تضمین می کند و اغلب مخزن ها یک شیر تخلیه میعانات دارند که به صورت دستی یا اتوماتیک عمل میکند.
این کالا نیز جز محصولات وارداتی و مورد تأمین توسط شرکت کارینا صنعت نمی باشد.
5. شلنگ ها و شبکه ی هوای فشرده
وظیفه ی این شبکه، توزیع هوای فشرده از کمپرسور به تمام مصرف کننده ها می باشد که اندازه این شلنگ ها و لوله ها در عملکرد سیستم تأثیر قابل توجهی در کیفیت و امنیت انجام وظایف سیستم دارد و بصورت کلی:
هر چه لوله ها طولانی تر باشند تلفات فشار هوا به دلیل اصطحکاک بیشتر است.
هرچه تعداد مصرف کنندگان متصل به لوله بیشتر باشد، لوله ها باید بزرگتر باشند.

کیفیت هوای فشرده
امنیت عملیاتی یک سیستم مبتنی بر هوا مستقیما به کیفیت هوای فشرده بستگی دارد و در حالت کلی هوای تمیزتر به علت کاهش خطرات ناشی از انسداد و سایش، امنیت عملیاتی سیستم را افزایش می دهد. کیفیت هوا طبق ISO 8573-1 :2010 استاندارد سازی شده است.
کلاس های مختلف آلایند ها و خلوص- استاندارد
ذرات ، روغن و آب مهمترین آلاینده ها در هوای فشرده هستند. برای هر یک از این سه، کلاس خلوص در استاندارد وجود دارد

کلاس های خلوص مطابق استاندارد ISO 8573-1
طبق تعریف، با کیفیت ترین هوای فشرده آن است که 100 درصد بدون روغن (کلاس 0) باشد. این کلاس خلوص در استفاده های پزشکی، صنایع غذایی و صنعت الکترونیکی مورد نیاز است.
هنگام طراحی یک سیستم هوای فشرده فاکتورهای محیطی را هم در نظر بگیرید. آلودگی هوا هنگام فشرده سازی غلیظ تر می شود. صنایعی که در نزدیکی محل مورد نظر ایجاد آلودگی می کنند تاثیر بسزایی در این مورد دارند. فاکتور های دیگر نظیر غلظت بالای اوزون می تواند روی سیستم تاثیر گذار باشد و به تجهیزات و مواد عایق (آب بند، هوابند) آسیب بزند، پس هیچ وقت شرایط اقلیمی را نادیده نگیرید.
بنابراین به منظور تضمین عملکرد ایمن در یک سیستم پنوماتیک مهم است که:
- بدانیم چه نوع هوایی وارد کمپرسور ما می شود.
- مطمئن شویم بعد از فشرده سازی، هوا خشک و تمیز باشد و روغن آن جدا شده باشد.
- تاثیرات شرایط محیطی نظیر آلودگی و آب و هوا را در نظر بگیریم.
- اجزایی که تحت بار زیاد کار می کنند به صورت منظم روانکاری شوند.
6. قسمت آماده ساز هوا:
- فیلتر
- رگلاتور فشار
- روان کننده
- شیر فعال ساز
7. شیرهای کنترل:
- شیر کنترل مستقیم
انواع دیگر شیر های کنترل
در مدار پنوماتیک لازم است مسیر و فشار هوا کنترل شود و به این منظور از شیرهای پنوماتیکی استفاده می شود. به طور کلی کنترل فشار یا کنترل میزان جریان با تغییر مسیر و جهت هوای فشرده است.شیرها بر اساس نوع طراحی در دسته بندی های متفاوت قرار می گیرند. شیرهای راه دهنده یکی از این دسته ها محسوب می شوند.از شیرهای راه دهنده به منظور قطع و وصل انرژی هوای فشرده استفاده می شود. این شیرها بر اساس تعداد دهانه ها (پورت) و تعداد وضعیتشان تعریف می شوند.
8. شیر های کنترل جریان، شیرهای چک:
- شیرهای کنترل جریان، یک طرفه یا دوطرفه
- تنظیم کننده جریان خروجی
- شیر های یکطرفه (چک ولو)
9. عملگرها، سیلندر ها:
- عملگرهای پنوماتیکی به دو گروه اصلی خطی و دورانی به صورت زیر تقسیم می شوند:
- عمگرهای خطی: سیلندر یک کارهو سیلندر دو کاره
- عملگرهای دورانی:موتور هوایی سیلندرهای هوایی
مقایسه عملگرهای متداول | ||
نوع عملگر | مزایا | معایب |
الکتریکی |
|
|
هیدرولیکی |
|
|
پنوماتیکی |
|
|
پنوماتیک
انواع سیلندر پنوماتیک:
· سیلندر یک طرفه
در این نوع سیلندر هوای فشرده فقط به یک طرف از سیلندر وارد شده و بر پیستون نیرو اعمال می کند، سمت دیگر سیلندر در این حالت به هوای آزاد متصل است، در این نوع سیلندر فقط در یک جهت کار انجام می دهد و عمل برگشت توسط نیروی فنر تعبیه شده در ساختمان داخلی عملگر و یا اعمال نیرو از بیرون امکان پذیر می گردد.
· سیلندر دو طرفه
سیلندر پهلو به پهلو از نظر ساختمان از دو سیلندر دو کاره متصل به هم که یک سیلندر واحد را به وجود می آورند تشکیل شده است که با استفاده از این آرایش با اتصال هوای فشرده در دو قسمت، نیروی قابل دسترس تقریباً دو برابر خواهد شد.
· سیلندر با میله پیستون دو طرفه
این نوع سیلندر میله پیستون در دو طرف دارد. در این روش یاتاقان بندی میله پیستون وضعیت مناسب تری خواهد داشت (به دلیل وجود دو یاتاقان) و نیروی قابل دسترس در حرکت رفت و برگشت یکسان خواهد بود، در این حالت میله پیستون را می توان تو خالی انتخاب نمود.
- سیلندرهای چند موضعی
سیلندرهای دارای چند میله پیستون از دو یا چند سیلندر دو کاره تشکیل می شود. هر سیلندر با اتصال به هوای فشرده به صورت مستقل کنترل می گردد.
- سیلندرهای ضربه ای
نیروی قابل دسترس توسط سیلندرهای نیوماتیکی محدود هستند. سیلندرهای ضربه ای جهت انجام کار از قابلیت تبدیل انرژی جنبشی ناشی از حرکت با سرعت زیاد استفاده می کنند.
- سیلندرهای دورانی
حرکت میله پیستون دو کاره که به یک چرخ دنده شانه ای متصل است، موجب چرخش محور چرخ دنده می شود و بدین ترتیب از حرکت خطی، حرکت دورانی نتیجه می گردد. حرکت دورانی در محدوده ی ۴۵ درجه، ۹۰ درجه، ۱۸۰ درجه، ۲۷۰ درجه تا ۳۶۰ درجه قرار دارد.
- سیلندرهای بدون میله پیستون
سیلندرهای فاقد میله پیستون از حيث ساختمان و عملکرد به سه نوع مختلف زیر تقسیم می گردند. سیلندر کابلی یا تسمه ای، سیلندر تسمه ای آب بندی شده و سیلندر با کوپلینگ مغناطیسی. در این سیلندر نیروی پیستون از طریق یک تسمه به لغزنده منتقل می شود.
- سیلندر با کوپلینگ مغناطیسی
این نوع سیلندر یک عملگر خطی دو کاره (سیلندر بدون میله پیستون) است که یک بدنه و دو پیستون لغزنده دارد. پیستون در داخل سیلندر در اثر تحریک نیوماتیکی آزادانه حرکت می کند ولی این پیستون اتصال ثابتی با خارج از سیلندر ندارد. پیستون و لغزنده به تعدادی دیسک مغناطیسی متصل هستند که سبب ایجاد یک کوپلینگ مغناطیسی شده اند. به محض ورود هوای فشرده به محفظه سیلندر و حرکت پیستون، لغزنده نیز به صورت هم زمان حرکت می کند.
· ساختمان سیلندر
- بدنه
- در پوش های ابتدا و انتها
- پکینگ های دو طرفه
- میله پیستون
- بوش یاتاقانی
- گردگیر میله پیستون
- اجزا اتصال دهنده و آب بندها
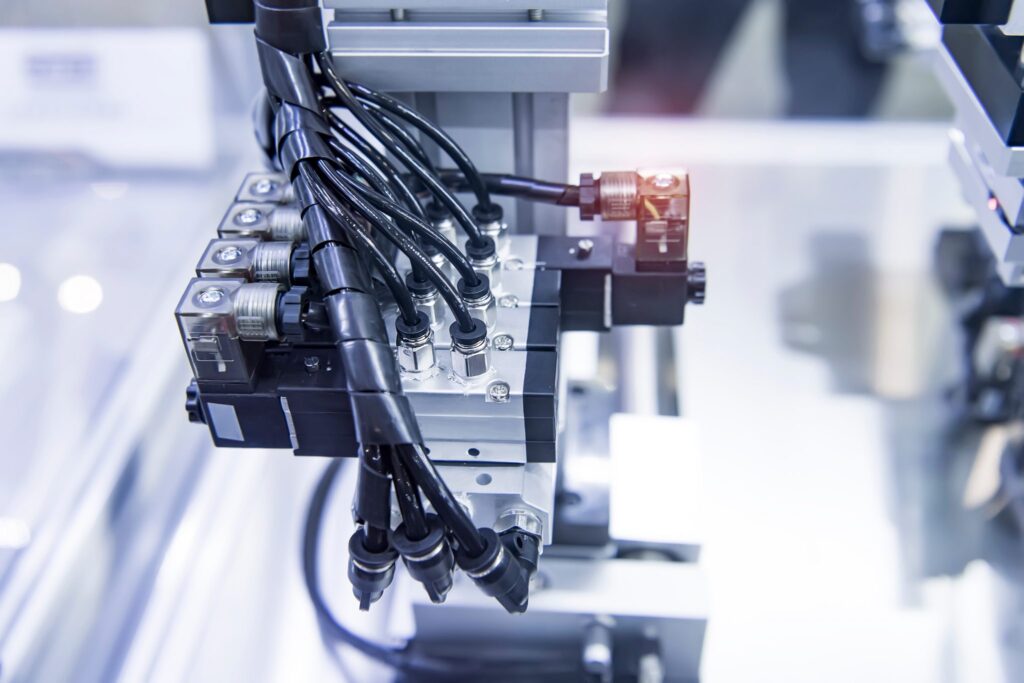
واحد مراقبت و فیلتر پنوماتیک
- فیلتر هوا
- رگولاتور فشار همراه با فشارسنج
- روغن پاش
- تعمیرات و نگهداری فیلترهای هوا در سیستم پنوماتیک
- به دلیل نفوذ گرد و غبار و رسوبات به منافذ فیلتر، باید هر چند وقت یکبار آن را تمیز نموده یا تعویض نمایید.سطح آب جمع آوری شده در کاسه فیلتر، قبل از آنکه به علامت ماکزیمم برسد باید تخلیه شود، در غیر این صورت آب تقطیر شده موجود در کاسه فیلتر، مجدداً وارد مسیر هوای فشرده خواهد شد.
- نحوه تخلیه آب جمع آوری شده در کاسه فیلتر هوای فشرده:اگر در یک مدت زمان کوتاه در کاسه فیلتر مقدار زیادی آب جمع شود، بهتر است از تخلیه اتوماتیک به جای تخلیه دستی استفاده نمایید.
